在鎧裝電纜的護套擠塑生產時,由于纜芯自重原因,在纜芯過模過程中纜芯外層鋼帶會與模芯內壁接觸,纜芯外層鋼帶會帶走部分熱量,且因都是金屬物之間接觸,導致傳熱速度快,從而使模芯內壁(模芯承徑段)溫度下降,導致護套料擠塑過程中容易出現塑化不良、皺皮、偏芯或脫料現象。且隨著環境溫度的下降,表面塑化不良質量缺陷越明顯,直接影響鎧裝電纜的產品質量。
(一)未改進前生產狀況描述
為了減少鎧裝電纜的護套擠塑生產時纜芯外層鋼帶會模芯內壁接觸,盡量使纜芯從中心位置進入機頭模芯:入模口處約400mm有一個支持纜芯導輪,整個機頭總長約560mm,機頭與水槽中第一個導輪間距有1米多,現有擠塑模芯是通孔,但由于纜芯自重的因素,很難保證纜芯擠塑時處于懸空狀態,從而纜芯在進模處會與模芯內壁接觸,且電纜外徑越大,鎧裝與模芯的接觸面積越大,傳熱越嚴重,導致擠塑模口處溫度低于材料的塑化溫度,在電纜的表面形成連續的塑化不良硬包、偏芯、皺皮等。
(二)改進后解決的技術問題
1、在擠塑模芯承徑段上距擠塑模外端25mm處設置一個高為1mm,傾斜角度為30°的臺階段,以減少鎧裝層與模芯內壁的接觸面積,從而減少鋼帶帶走的熱量;
2、增大擠塑模套的內徑(模芯外徑與模套內徑配模比值由原來的標稱厚度的3.5倍調整到5倍),以增大擠塑模承徑段塑料的熱慣量。
通過以上兩點的改進,確保鎧裝電纜護套擠塑時模口溫度不低于材料的塑化溫度,從而徹底解決鎧裝電纜護套擠塑生產時因鋼帶傳熱導致的塑化不良、皺皮、偏芯或脫料等質量缺陷。
(三)生產過程示意圖
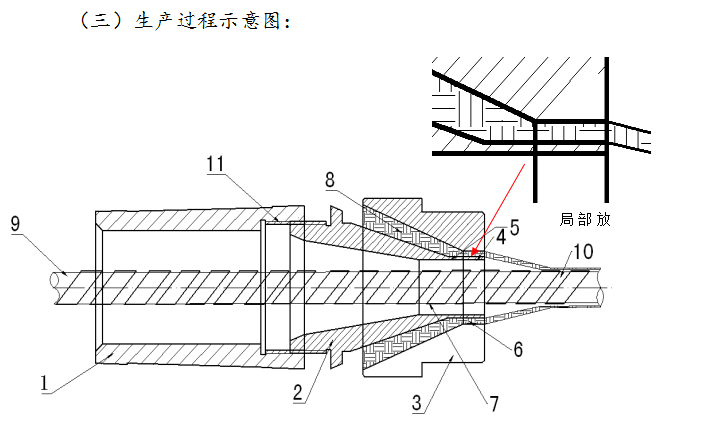
修改前加工示意圖
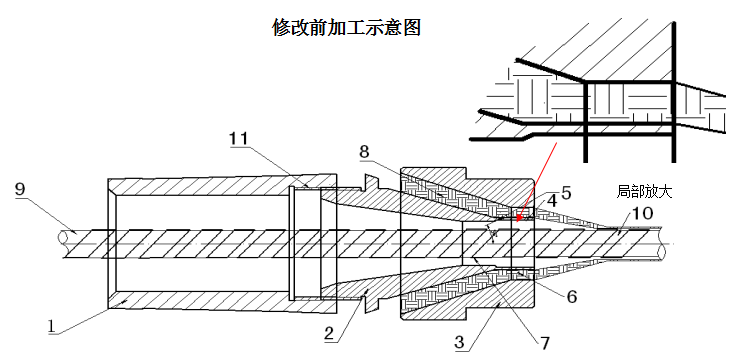
修改后加工示意圖
1、模芯座 2、擠塑模芯 3、擠塑模套 4、模芯定徑區 5、模芯嘴內壁30° 斜角臺階 6、模套定徑區 7、纜芯雙層間隙繞包鋼帶鎧裝層 8、模芯與模套間填充的擠塑材料 9、纜芯進線 10、擠塑完成后的成品電纜 11、模芯座與模套的連接部位
(四)對擠塑過程說明
1、生產過程示意圖中是電纜在擠塑過程中理論進線,在實際生產中操作人員能確保進線在中軸線位置,由于電纜的自重以及進線到出線的懸空造成電纜出線會偏下緊貼模芯內壁。
2、模芯定徑區總長為45mm, 模芯嘴內壁30°臺階設置在離模芯外端25mm。
3、生產時模芯座尾端會加增加支持導輪裝置,將電纜過線位置與中機頭的中心位置保持一致。
4、增加的30°1mm臺階位置,將電纜的進線在25mm處抬高墊,使電纜的鎧裝多屬層與模芯有間隙,保持擠出塑料的塑化不良問題。
(五)模芯示意圖
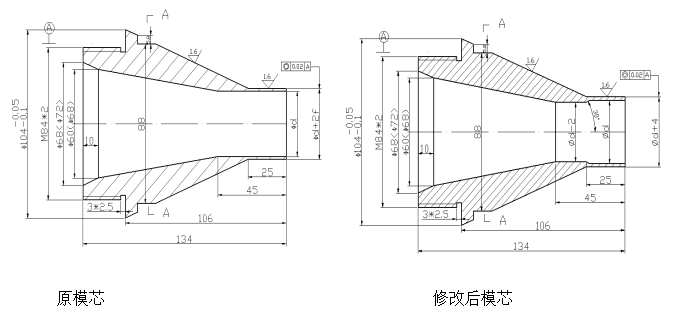
(六)有益效果通過對擠塑模芯的內部結構進行調整及放大模套內徑與模芯外徑的差值,有效地解決了鎧裝電纜護套擠塑生產時因鋼帶傳熱導致的塑化不良、皺皮、偏芯或脫料等質量缺陷,提高了金屬層鎧裝電纜護套擠塑表面質量,降低環境溫度過低對擠塑表面的影響。 (李淵峰 潘春梅) |