超導電纜作為新一代電力傳輸技術,憑借零電阻、低損耗、大容量的特性,成為破解城市核心區供電瓶頸、推動電網綠色轉型的“利器”。然而,其運行依賴極端低溫環境(約-196℃)和精密控制系統,涉及低溫維持、失超保護、機械適配等多重技術挑戰。下面將從核心問題與應對實踐“如何穩”、標準化運行流程“如何做”、典型問題與解決措施“如何修”三個維度展開,結合實際案例,系統闡述超導電纜的運行要點與實踐經驗。
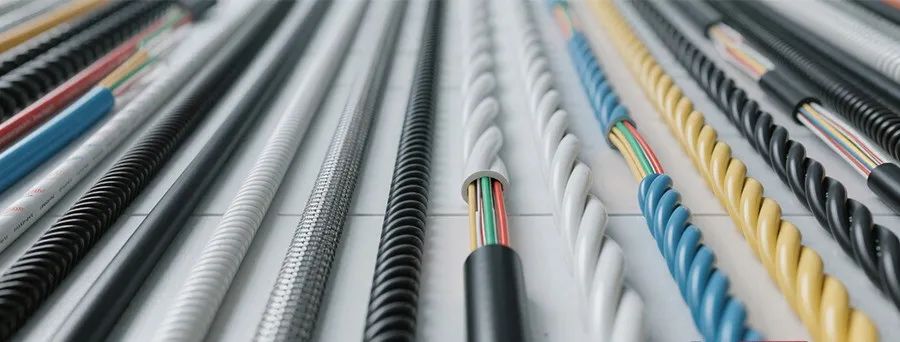
一、超導電纜運行的核心問題與應對實踐
(一)低溫環境維持:液氮系統的穩定是運行的“生命線”
超導材料需在液氮環境(-196℃)下才能呈現零電阻特性,因此維持低溫環境是首要任務。核心挑戰在于:液氮循環系統的漏熱控制(環境熱量侵入會導致液氮汽化,破壞低溫條件)、制冷機的高效運行(需持續補充冷量)以及系統壓力與流量的動態平衡。
應對實踐:
1. 多層絕熱設計:采用雙層柔性真空絕熱管包裹電纜本體,減少外部熱量侵入(如上海35kV示范工程的絕熱管設計,熱損耗僅為傳統電纜的1/10);
2. 多機并聯制冷系統:配置多臺制冷機并行運行,根據冷量需求動態調整開啟臺數(深圳10千伏項目采用國產大冷量GM制冷機,解決了微小空間高效換熱難題);
3. 實時監測與冗余備份:在電纜入口、出口及制冷機關鍵節點部署溫度、壓力、流量傳感器(上海工程設置9處工作井,每處配備液氮監測設備),一旦發現異常(如溫度超±2℃),立即啟動備用制冷機,確保低溫環境穩定。
(二)失超保護:從“被動斷電”到“主動自恢復”的技術跨越
失超(超導材料因溫度、電流或磁場超過臨界值,突然恢復電阻的現象)是超導電纜最嚴重的運行故障,可能導致局部過熱、絕緣損壞甚至設備燒毀。傳統保護方式依賴快速斷電,但會導致供電中斷,影響用戶體驗。
應對實踐:
1. 多參數融合監測:通過光纖測溫、電流傳感器、電壓互感器實時采集電纜溫度、電流、電壓數據(深圳項目在400米電纜沿線部署光纖測振震裝置,實現毫米級溫度感知);
2. 智能失超保護裝置:研發“失超-跳閘-自恢復”一體化裝置,當檢測到電阻突增(如超過0.1mΩ),裝置在10毫秒內切斷故障電流,并通過制冷系統快速降溫,使超導材料重新進入超導態(上海工程的保護裝置已實現3次失超后自恢復,未影響用戶供電);
3. 電磁環網設計:在電網側構建冗余供電路徑,失超期間通過環網切換維持供電(深圳項目接入福田中心區雙電源環網,失超時負荷轉供率達100%)。
(三)機械性能適配:敷設與運行中的“柔性挑戰”
超導電纜由超導帶材(僅0.4毫米厚)、緩沖層、保護層等多層結構組成,其機械強度遠低于傳統銅纜。敷設時牽引力過大、彎曲半徑過小或運行中振動,均可能導致帶材斷裂或層間剝離。
應對實踐:
1. 定制化敷設工藝:通過1:1模擬試驗確定關鍵參數(如上海工程在閔行區吳涇鎮復現中心城區復雜環境,測得超導電纜最大允許牽引力為8kN,最小彎曲半徑為1.5米);
2. 專用敷設設備:研發小轉角大落差敷設器具(如深圳項目采用“泥水平衡頂管”與“大角度繞行”工藝,解決了老城區地下管廊狹窄問題);
3. 動態應力監測:在敷設過程中實時監測電纜張力(深圳項目使用光纖光柵傳感器,張力偏差超過±5%時自動報警),并在運行中通過智能地釘監測振動(上海工程9處工作井均安裝振動傳感器,振動頻率超10Hz時啟動減震措施)。
(四)絕緣與熱管理:“低溫+高壓”的雙重考驗
超導電纜運行于液氮環境(-196℃),同時需承受35kV甚至更高電壓,絕緣材料需兼具低溫韌性與高壓耐受性。此外,電纜終端(連接常規電網的接口)因漏熱可能產生局部高溫,影響絕緣性能。
應對實踐: 1. 復合絕緣設計:采用固體絕緣材料(如環氧樹脂)與液氮的復合絕緣結構(上海35kV電纜的絕緣層厚度僅20mm,耐電暈能力達傳統電纜的2倍); 2. 終端絕熱優化:終端采用真空多層絕熱結構(深圳項目終端漏熱率低于0.5W/m,比國際標準低30%),并在接口處填充低溫膠,防止液氮汽化導致的絕緣間隙; 3. 定期絕緣測試:每季度使用兆歐表測量主絕緣電阻(要求≥1000MΩ),每年進行介質損耗測試(上海工程三相介質損耗因數均<0.5%,遠低于1%的警戒值)。
二、超導電纜的標準化運行流程
超導電纜的運行需嚴格遵循“預冷-試驗-并網-運維”四階段流程,每一步均需記錄關鍵參數,確保可追溯性。
(一)預冷階段:從常溫到-196℃的“漸進式降溫”
預冷是啟動運行的關鍵步驟,需避免因降溫過快導致的熱應力損傷(如超導帶材斷裂或接頭脫落)。
具體流程為:
1. 系統抽空:用真空泵將電纜內部管道真空度抽至1×10⁻³Pa,排除雜質(如水分、空氣),防止低溫下堵塞管道;
2. 氮氣吹除:用室溫氮氣緩慢吹掃管道(流量≤5m³/h),進一步清除殘留雜質;
3. 液氮預冷:以0.5℃/min的速率注入液氮,逐步降低電纜溫度(上海工程預冷耗時48小時,最終溫度穩定在-196℃±2℃)。
(二)通流試驗:驗證額定載流能力的“實戰演練”
預冷完成后,需通過通流試驗驗證電纜的通流能力。
試驗采用“電流疊加法”:
1. 電纜末端三相短路,首端接入調壓器,逐級增加電流(從10%額定電流開始,每30分鐘增加10%);
2. 監測各相電壓、電流相位(要求相位差≤5°)、溫度(液氮出口溫度≤-190℃);
3. 當電流達到額定值(如上海35kV電纜額定電流2160A)并穩定24小時后,試驗合格。
(三)并網運行:“在線監測+智能運維”的全天候保障
并網后需通過在線監測平臺實時監控以下參數:
1. 液氮系統:入口壓力(0.3-0.5MPa)、出口溫度(-196℃±2℃)、流量(10-15L/min);
2. 電氣參數:電流(≤額定值)、電壓(±5%額定電壓)、介質損耗(≤1%);
3. 環境參數:工作井溫濕度(溫度≤30℃,濕度≤70%)、振動(≤5Hz)。 運維團隊采用“立體巡檢+集中監控”模式:每日人工巡檢工作井(檢查絕熱管是否結霜、制冷機運行聲音是否異常),每周分析在線監測數據(如液氮流量波動超過±10%需排查管道堵塞),每月進行紅外測溫(終端溫度≤-180℃為正常)。
(四)定期檢修:“狀態評估+部件更換”的預防性維護
每運行1年需進行全面檢修:
1. 絕緣性能評估:測量主絕緣電阻(≥1000MΩ)、介質損耗因數(≤0.5%);
2. 機械性能檢查:通過X射線檢測超導帶材是否有裂紋(上海工程運行3年未發現帶材損傷);
3. 制冷系統維護:更換制冷機油、清洗換熱器(深圳項目制冷機維護周期為2000小時)。
三、運行中可能出現的問題及應對措施
盡管技術不斷優化,超導電纜運行仍可能因環境變化、設備老化或操作失誤出現故障,需針對性制定應對策略。
(一)問題1:液氮溫度異常升高(如出口溫度>-190℃)
原因:絕熱管漏熱(如真空層破壞)、制冷機故障(如壓縮機磨損)、液氮泵堵塞(雜質堆積)。
應對:
1. 立即檢查絕熱管外觀(結霜區域可能為漏點),使用真空計測量絕熱層真空度(<1×10⁻²Pa為正常),若漏點較小,用低溫膠密封;若漏點較大,更換絕熱管;
2. 切換至備用制冷機(上海工程配置2臺主制冷機+1臺備用機,切換時間<5分鐘);
3. 關閉液氮泵,用氮氣反吹管道(壓力0.2MPa),清除雜質(深圳項目曾因施工遺留銅屑堵塞管道,反吹后恢復正常)。
(二)問題2:失超觸發(電阻突增>0.1mΩ)
原因:過電流(如用戶負荷突增)、局部過熱(帶材焊接點接觸不良)、磁場干擾(附近有大型電機)。
應對:
1. 保護裝置自動跳閘(深圳項目跳閘時間<10ms),切斷故障電流;
2. 檢查電流記錄(若因負荷突增,聯系用戶調整用電計劃;若因焊接點問題,重新焊接并測試電阻);
3. 啟動制冷機加速降溫(目標溫度-196℃),待電阻恢復至0后重新并網(上海工程曾因負荷突增觸發失超,30分鐘后自恢復供電)。
(三)問題3:敷設后電纜帶材斷裂(如絕緣電阻<100MΩ)
原因:牽引力過大(超過8kN)、彎曲半徑過小(<1.5米)、側壓力過高(>5kN/m)。
應對:
1. 立即停止敷設,使用光纖檢測斷裂位置(精度±1米);
2. 截斷斷裂段,更換備用帶材(需與原帶材型號一致),重新焊接并做絕緣處理(深圳項目曾因彎曲半徑過小導致帶材斷裂,更換后測試合格);
3. 調整敷設參數(如降低牽引速度至0.5m/min,增大彎曲導向輪直徑)。
超導電纜運行的“技術+管理”雙輪驅動
超導電纜的穩定運行依賴于低溫維持、失超保護、機械適配、絕緣熱管理四大核心技術的突破,以及預冷-試驗-并網-運維標準化流程的嚴格執行。實際應用中,通過智能監測、冗余設計和快速響應機制,可有效應對溫度異常、失超、機械損傷等問題。隨著上海、深圳等示范工程的成功,超導電纜已從實驗室走向商業化,未來將在超大城市電網升級、可再生能源消納等領域發揮更大作用。(來源:中國線纜網) |