1 概念
絞線就是將若干單線按照一定的方向和規則扭絞在一起,成為一個整體線芯的工藝。
2 特點
2.1 柔軟性好廣義上說,金屬線越細,柔軟性越好。絞線由許多細金屬線構成,因此比較柔軟。但是,絞線的柔軟性與絞合時所選的工藝參數有大的關系。
絞線的柔軟性與下列因素有關:
同截面絞線,所用單線根數越多即單線越細,柔軟性越好。
結構相同的絞線,一般情況下相應絞層的節距越小越柔軟。
要使導線更加柔軟,可以采用復絞。
2.2 可靠性高用單線做電纜導體時,受制造過程產生的缺陷和材料不均勻性影響而會降低單根導線的可靠性。用多根單線絞合的線芯,缺陷得以分散,導線的可靠性明顯提高。
2.3 強度大相同截面積的絞線和單根導線相比強度要大得多。
2.4 穩定性好絞線彎曲時,每一根單線的位置輪流處在絞線上部伸長區和下部的壓縮區,單線不會產生伸長和壓縮,也不會發生單線位置移動,結構具有良好的穩定性。
2.5 減少渦流損耗,提高輸電效果
3 絞線的形式
3.1 正規絞合就是把單線或股線按同心圓的方式,相鄰層絞向相反,分層有規則地絞合在絞線軸線周圍的絞合方式。
3.2 非正規絞合非正規絞合方式包括束絞、特殊絞合(扇形、半圓形、瓦形線芯)、圓形緊壓線芯、型線絞合等。
4 工藝參數
4.1 絞合方向紋合方向分為右向與左向。絞合方向一般裸絞線最外層為右向,導電線芯最外層為左向 方向判斷:可用左手或右手將手掌向上,拇指叉開,其余四指并攏,并攏的四指順向絞線軸向,如果右手拇指的斜向與單線的斜向一致,就是右向(z向),如果左手拇指的斜向與單線的斜向一致,就是左向(S向)。
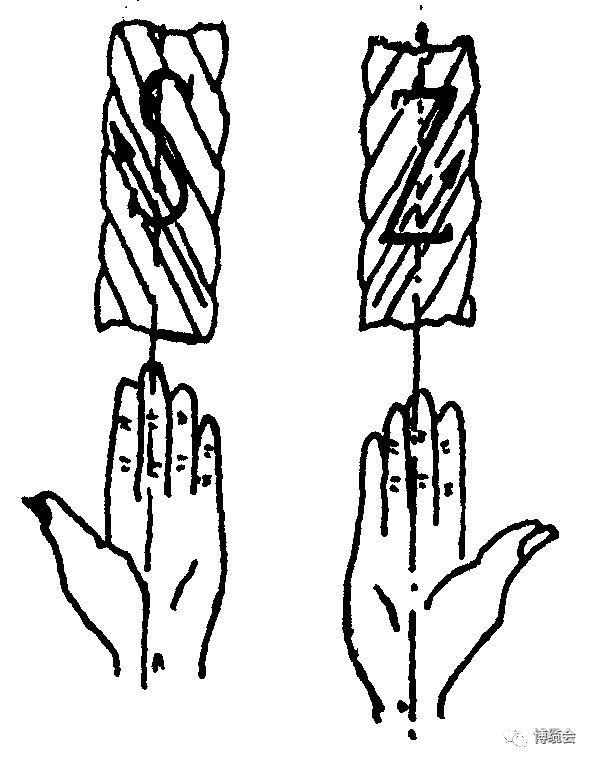
4.2絞合節距測量
束線產品節距測量,可用實測法,即取出一段束線產品,剪斷表面的一根并在剪斷處作好標記,以束線相反方向拆去10個螺旋,然后用直尺測量拆去10個螺旋部分絞線的長度,再將所得長度數據除于10,即可得出該束線的節距長度 。
4.3 節距比
絞線的節距比是指絞線節距長度與絞線的直徑之比,即節距為直徑的倍數。節距比愈小,柔軟性愈好;各根單線之間的空隙愈小,即絞合得愈密實;而且節距與單線在一個節距的實際長度相差也愈大,同樣長度絞線所使用的單線長度也就愈長。
絞合節距是由線速度和絞籠轉速決定的。
絞線機:h=V/n*1000 (mm)
雙節距束線機:h=V/2n *1000(mm)
式中:h——絞合節距mm
V——出線速度 米/分
N——絞籠轉速 轉/分
線速度固定時,絞籠轉速快,絞合節距小;絞籠轉速慢,絞合節距大;即絞線機牽引速度恒定,節距與絞籠轉速成反比。如果絞籠轉速固定時,絞合節距大,線速度快;絞合節距小,線速度慢,即絞籠轉速不變時,線速度與絞合節距成正比。
4.4 絞入系數
在絞線的一個節距內,單線實際長度與絞線節距長度之比稱為絞入系數,以K表示,其值為K=l/h。絞入系數與節距比的平方成反比。
4.5絞入率
就是在一個節距內,單線實際長度和絞線節距長度的差值與絞線節距長度之比率。計算公式為K=L-h/h*100%
4.6絞線的外徑
絞線的外徑就是外層單線與之相內切的圓的直徑。
中心層單線根數不同時的絞線外徑

4.7 絞線的緊壓緊壓絞線是在同心層絞的基礎上再用一定孔型的壓輥緊壓而制成。緊壓工藝有一次緊壓和分層緊壓兩種。
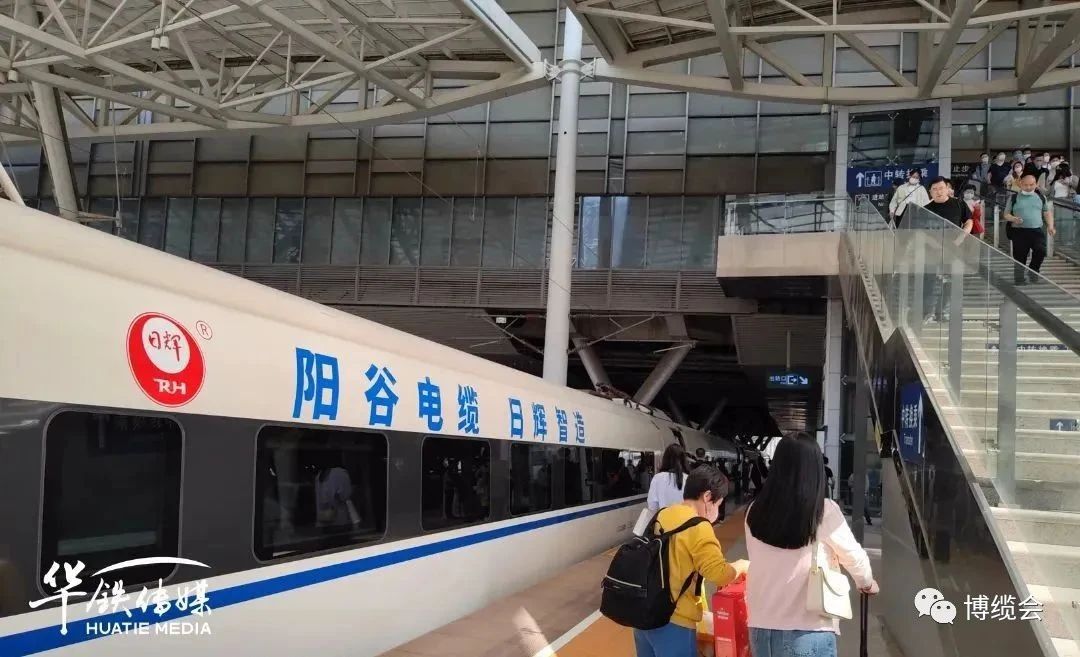
5 質量控制
5.1 準備階段
在未裝夾單線或股線前,應根據設備檢查的要求,檢查設備情況。必要時啟動設備進行試運行,檢查各相關部件的運行情況,各類保護開關是否有效。
檢查各類領用材料是否符合工藝指導卡規定和生產計劃的要求,如單線的規格、長度等等。
按工藝要求將將單線或股線安置到放線架上,注意內外層絞向、排列等應與工藝要求一致。預調好放線張力以及收線張力等。
根據生產指令和工藝要求選配并安裝好各類摸具,如壓輪、緊壓模等,必要是根據實際情況進行適當調整。收線盤的容量應與生產長度和規格相適應,裝夾時應按設備的操作規程進行。
5.2 運行階段設定好絞合節距和絞合方向,將單線或股線逐步穿好并與導引繩連接引入到收線盤。低速啟動設備,運行一定長度,停車后檢查節距、絞向等。同時對設備的運行情況再作一檢查,以確定完好。待確認符合要求后再正常開車運行,在運行過程中,不得私自離崗,因巡回檢查絞線外徑、查看絞線是否有缺股、斷絲、外觀等并按半成品檢驗規范要求記錄。成品不允許整體焊接,單線直徑0.20mm及以下者允許扭接,0.2mm以上者應采用焊接。排線的節距應與絞線尺寸和收線速度相適應,嚴禁嚴重的交叉排列。線盤不能裝得過滿,一般應低于盤邊不小于20mm為宜,卸盤時應注意防止碰傷線芯。
5.3 絞線完工階段對每盤下機后的線芯應認真填寫流水卡及各類報表,以確保半制品流轉質量。對每盤線芯下車后應再次核實是否符合要求,并按指定地點堆放。工作結束后應關閉電源,以防止他人誤操作引起設備故障。除現場多余的材料,以防止混用。如遇交接班,應將本班運行情況和未完成情況如實移交下班接班人。
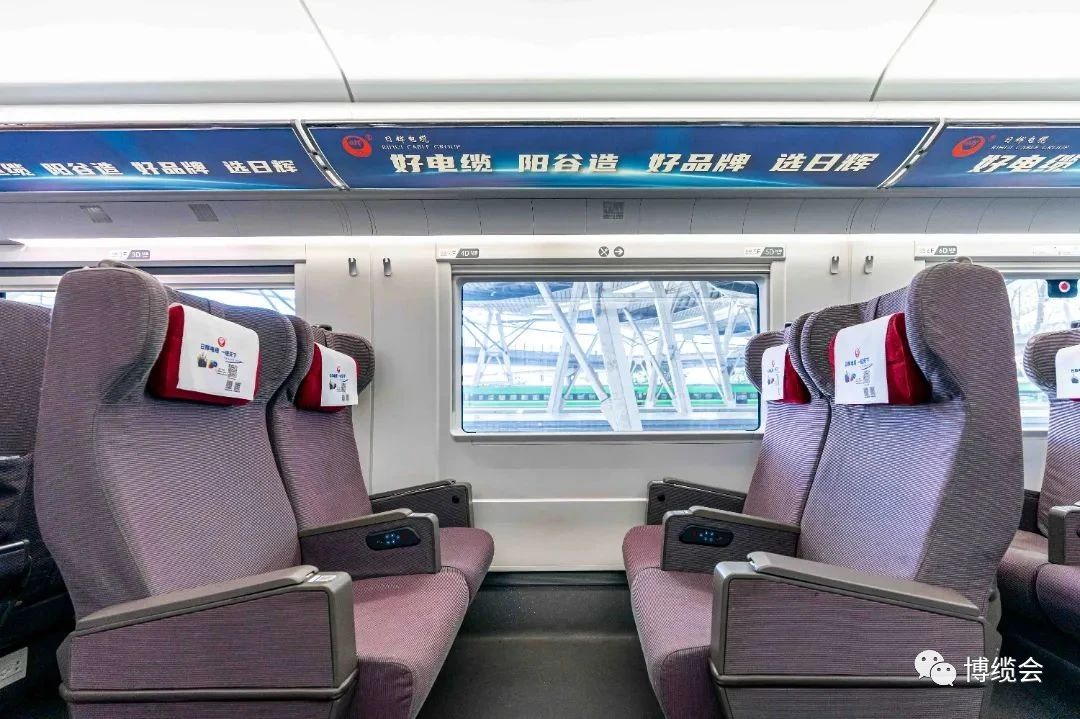
6 質量標準
6.1 束線
1) 外觀 :絞合后的束線,單線表面應光潔,無明顯的機械損傷,不得有氧化變色現象,不得有明顯的松股和背股。對于鍍錫線芯,表面要求色澤均勻、光滑,不能有黑斑,鍍錫層均勻,不應有漏鍍等;
2) 尺寸:單線應圓整,不應有明顯的拉細現象,拉細必須在標準規定的范圍內,束線外徑應在工藝要求以內;
3) 結構與組成:束線不得有缺根、斷根、松股,搭股、束線表面如有輕微擦毛,仍可作合格品。結構與組成必須符合工藝規定;
4) 束線的節距比和束制方向應符合規定;
5) 焊接:成品束線不允許整體焊接,單線及股線允許焊接,其中單根單線焊接,直徑0.20mm及以下者允許扭接,0.2mm以上者應采用冷焊鉗焊接,相鄰兩個接頭之間的距離應不小于300mm,股線整根焊接采用銀焊片,焊接要牢固可靠;
6) 銅導體必須是退火狀態;
7) 束制產品成品直流電阻值 :符合GB/T 3956-2008;
8) 裝盤 :成盤導電線芯排線整齊,平整,不得有腰鼓形和線芯互相壓疊現象。
6.2 絞線
1) 外觀 :絞線外觀應光潔,不得有三角口、裂紋、斑疤及夾雜物,節距均勻整齊,不得有明顯的機械損傷,對于銅絞合導體不得有氧化變色現象和黑斑。對于鍍錫線芯要求色澤均勻,光亮,不得有黑斑和漏鍍;
2) 尺寸:單線應圓整,不應有明顯的拉細現象,拉細必須在標準規定的范圍內,絞線外徑應在工藝要求以內;
3) 結構與組成:應符合GB/T 3956的規定。不能缺根,少股、斷股、壓疊,對扇形線芯壓型的偏心度不能超過10%;
4) 絞線的節距和絞合方向應符合規定。多層絞線由內至外節距比逐漸縮小,且同層節距保持一致,絞合各層應相反; 5) 焊接:架空絕緣電纜導體中的單線7根及以下均不允許有接頭,7根以上的絞線中單線允許接頭,接頭應牢固和修光,接頭處直徑應與原單線直徑相當且不應打彎,在同一單線上或整根絞線上任何兩個接頭間的距離應不小于15m;鋼芯加強型導體中鋼芯不允許有任何接頭。第2種導體不允許整體焊接,塑料絕緣電纜(電線)導體中的單線允許接頭,接頭應牢固和修光,接頭處直徑應與原電線直徑相當且不應打彎,在同一單線上或整根絞線上任何兩個接頭間的距離應不小于300㎜;6) 除架空絕緣線用硬銅導體外,其余銅導體必須是退火狀態;7) 成品直流電阻值 :符合GB/T 3956-2008 ;8) 裝盤 :成盤導電線芯排線整齊,平整,不得有腰鼓形和線芯互相壓疊現象。
7 絞線產品的質量缺陷和預防
7.1 過扭產生的原因:一是絞線在牽引輪上繞的圈數不夠,一般少于4圈,摩擦力過小而打滑,造成扭絞過度。二是收線張力松或收線盤不轉,而轉體仍在旋轉,而造成扭絞過度。單線在絞合時斷線,缺股單線斷線由于放線張力過大拉斷線芯。單線在拉制時松亂、排線不好、壓線跨線,造成線芯掙斷。單線本身材質有裂紋,機械性能不好脆斷。放線盤安裝位置不當,軸向晃動,造成斷線。單線跳出滑輪槽,機械卡斷。
7.2 絞線表面擦傷,刮傷線芯產生原因:通常一是分線盤上的線嘴磨損,二是單線跳出滑輪,三是穿線用木管或塑料管磨通,四是牽引設備推線板上的定位銷損壞,五是壓模中有異物等原因。
7.3 束線、絞線中單線背股、松股產生原因:一是放線張力不均勻,松松緊緊,張力松的線芯走得多、造成背股,二是壓模孔型太大,起不到適當調節張力的作用,三是壓模位置不當,絞合角不合理,四是節距比較大等。
7.4 絞線中單線起槽或表面缺陷產生原因:單線表面的麻坑、斑疤、三角裂、夾渣等缺陷,主要是材料帶來的,當然線芯表面有碎裂現象,也不排除拉線模孔型不合理而產生的
7.5 單線線徑忽大、忽小或摻錯線芯產生原因:絞合中發現單線線徑超差或摻錯線芯,主要原因是沒有認真執行工藝規定,另一個原因是管理上存在一定的問題。
7.6 絞合線芯松股產生的原因:
(l)節距過大,造成絞合線芯不堅實。
(2)壓模孔型過大,起不到壓實和調節作用。線模喇叭口過大或被磨損,損壞。
(3)放線張力不均勻,松松緊緊。
(4)各層節距比配合不好。(5)線芯狀態不符合工藝規定,尤其是鋁線芯。
(6)分線器和壓模座的位置不當等。
7.7 絞合線芯呈蛇形
產生的原因:大截面的絞合線芯和鋼芯鋁絞線芯容以發生蛇形彎的現象,主要是線芯芯子線的絞合存在問題,尤其是太硬的鋼絲,加上張力沒有調整好,分線不好,壓模又不起壓實的作用時,容易發生。
7.8 電線電纜用導體直流電阻不合格
大體原因是:一是線芯截面偏小,即生產中截面偏差小于負公差;二是線芯的狀態不穩定(鋁線H6-H9狀態混用,銅線軟硬不均);三是生產中工藝路線不規范(沒有定原材料的種類、沒法固定生產設備);四是成品測量時長度誤差超過0.5%;五是成品測量時,電纜導體溫度和環境溫度不平衡,誤差較大。六是線芯結構不合理(主要是指緊壓線芯)等 。
7.9 絞合方向錯,絞合節距不合格
7.10 排線混亂、壓線
(作者:曲超 來源:博纜會) |